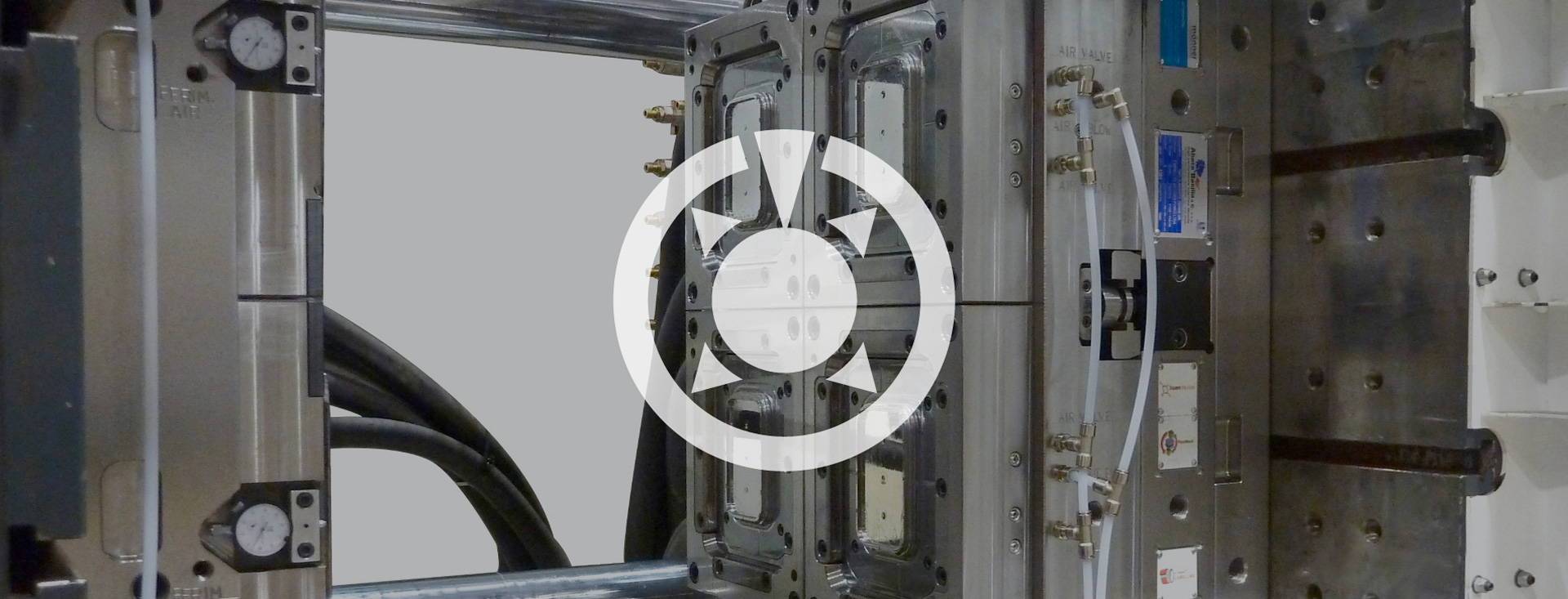
injection compression
The injection compression technology exploits two different stages of the injection machine to form the piece. The first stage consists of the injection trough the screw of the IMM while the second stage relates to the plasticization of the piece, due to the surfaces of the mould coming in contact with each other during the closing of the IMM. This second stage is the innovative part of the process.
The injection compression technology allows to form the pieces through these two different stages and above all, as a result of the plasticizing stage, it is possible to obtain pieces with enhanced properties.
Then there is a further advantage, which is obtained by injecting the plastic with a much lower injection pressure compared to the traditional injection technology; in fact using this new method the plastic material can be injected when the mould is still open, allowing it to flow into the cavity with much lower injection pressures. This reduces the stress to which the plastic is subjected.
The reduction of the stresses caused by compression together with a reduced stress on the plastic achieved by means of a lower injection pressure ensure improved resistance properties to the piece.
This results in a reduction of the weight under equal resistance conditions or in a greater resistance under equal weight conditions.
Processes
Thanks to its technology, flexibility and analytical approach, Abate Basilio does not only manufacture high performance moulds for the injection of plastic materials, but also provides customized solutions for any project. Thanks to the control of the entire production chain, from planning to delivery, each mould ensures unique quality, durability and performance.
Analysis
and planning
Abate offers a service of consultancy and analysis of the customer’s needs specific for each project. A specific technical knowledge is required for each sector, from food industry to chemicals, logistics etc., in order to be able to design and manufacture the more appropriate mould for a specific product.
Construction
and testing
Our production line includes 5-axis machining centres with fully automatic tool and pallets changers which allow us to achieve maximum repeatability and quickest throughput. Our machines are equipped with a laser control of the real dimensions directly obtained during the process in order to achieve the maximum precisions.
Maintenance
and after-sale
Our technical department ensures a fast, reliable and precise after-sale service. 95% of the company production is destined to be exported to different countries located over 5 continents. Our company has always given support to customers all over the world thanks to reliable planning of the mould and availability of spare parts which are guaranteed for 20 years.